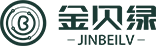
咨詢熱線:18151922896
聯(lián)系電話:025-84312185
傳真:025-84312185
網(wǎng)址:
郵箱:juhangvsr@163.com
地址:南京市光華路156號
【關(guān)鍵詞】振動時效,再生器,焊縫,殘余應(yīng)力,測試
【論文摘要】重油催化裝置再生器器壁焊縫附近多處出現(xiàn)貫穿性裂紋,其原因是應(yīng)力腐蝕開裂。通過振動時效處理以降低焊縫殘余應(yīng)力,可避免應(yīng)力腐蝕開裂的產(chǎn)生。因容器質(zhì)大體高,采用4點振動,*大主振力,減小附振力,延長振動時間的處理工藝。測試表明,新焊縫無論在垂直方向還是在平行方向的殘余應(yīng)力均降低了50%以上。大型工件采用振動時效處理降低焊縫殘余應(yīng)力效果顯*,并可大大縮短檢修工期。一年多以來設(shè)備運行正常。
大慶石油化工總廠煉油廠重油催化裝置再生器經(jīng)過5年多的運行,容器器壁焊縫附近多處出現(xiàn)貫穿性裂紋。經(jīng)分析和論證其成因為應(yīng)力腐蝕開裂。在應(yīng)力腐蝕開裂產(chǎn)生的3個因素即操作介質(zhì)、操作溫度和應(yīng)力中,只要控制其中一個,就不會產(chǎn)生應(yīng)力腐蝕裂紋。根據(jù)再生器運行情況,采用降低焊接殘余應(yīng)力方法來避免應(yīng)力腐蝕開裂的產(chǎn)生。若采用常規(guī)電加熱熱處理方法,熱處理溫度很難控制在工藝要求范圍內(nèi),同時又受工期限制。
為此對再生器焊縫裂紋采取先挖補(bǔ)焊接消除其原有裂紋,然后再進(jìn)行振動時效處理,便可降低焊縫殘余應(yīng)力。采用這種方法可降低或均化焊件內(nèi)部的殘余應(yīng)力,減少焊件變形,防止或減少由于熱處理和焊接產(chǎn)生的微觀裂紋,效果顯*。振動時效機(jī)理振動消除應(yīng)力實際上是利用周期性的動應(yīng)力疊加,使局部產(chǎn)生塑性變形而釋放應(yīng)力。振動時效處理時,通過激振器對被處理金屬工件施加一個交變應(yīng)力,如果交變應(yīng)力幅與被處理金屬工件上某些點存在的殘余應(yīng)力之和達(dá)到材料的屈服*限時,這些點將產(chǎn)生晶格滑移。盡管宏觀上沒有達(dá)到屈服*限,但同樣會產(chǎn)生微觀塑性變形,而且這種塑性變形往往首先發(fā)生在殘余應(yīng)力*大點上,使這些點受約束的變形得以釋放,從而降低殘余應(yīng)力。根據(jù)上述機(jī)理和大量實踐表明,振動時效的一個突出特點是:高應(yīng)力降低的比例大,特別是在應(yīng)力集中處,殘余應(yīng)力降低較快。國內(nèi)研究表明,采用振動時效降低和均化了焊接殘余應(yīng)力,因而提高了構(gòu)件的抗應(yīng)力腐蝕能力。
振動時效處理工藝:該重油催化再生器質(zhì)量達(dá)800t以上,由于是現(xiàn)場檢修,整個塔身固定在地基上,而且設(shè)備高達(dá)50m,*大直徑達(dá)8m(不包括外側(cè)平臺),*小直徑也有5.2m,如圖1所示(圖中Ⅰ、Ⅱ、Ⅲ、Ⅳ為時效振動儀振動塊的位置)。這是目前我國振動時效處理的*大設(shè)備,所以不能采用常規(guī)的振動時效處理方法——用減震橡膠墊將工件與地面分開,以減少振動能量損失,而是采用多點(共分4點)振動(見圖1),加大主振激振力,減小附振激振力,以及延長振動時間的方法,對其進(jìn)行振動處理。 圖1 再生器結(jié)構(gòu)及激振點位置示意圖
1、激振點的選擇本次振動時效選用JH-7OOA智能頻譜諧波交流振動時效裝置,激振點選擇在工件易起振部位。對于長形工件,一般選擇中間或兩端;對于小直徑的筒體工件來說,需在中間選一點。但該再生器*小直徑為5.2m,故選擇對稱三點,即Ⅰ、Ⅱ、Ⅲ點;選擇Ⅳ點是為了確定更好地消除附近焊縫的殘余應(yīng)力,但在實際操作過程中選擇Ⅰ、Ⅱ、Ⅲ點已能滿足振動時效要求。所以,只在*Ⅳ點附近振動了20min。
2、振動頻率n振的選擇振動時效以主振n主為主,附振n附為輔。固有頻率n固振幅峰值的1/3~2/3處對應(yīng)的頻率為振動頻率。實際操作時,選n振=n固-100。
3、工藝參數(shù)的選擇 Ⅰ、Ⅱ、Ⅲ三點的固有頻率接近,所以均采用相同的參數(shù),見表1。Ⅳ點的振動參數(shù)見表2。表1 Ⅰ、Ⅱ、Ⅲ點振動工藝參數(shù)主振 主振頻率(r/min) 激振力(%) 振動時間(min) 3540 70 10 附振 附振頻率(r/min) 激振力(%) 振動時間(min) 5170 50 20 表2 Ⅳ點振動工藝參數(shù)附振頻率(r/min) 激振力(%) 振動時間(min) 5280 50 20 焊縫殘余應(yīng)力測試
用振動時效法處理再生器修復(fù)焊縫后,再采用JH-80三維應(yīng)力分布磁測系統(tǒng)對修復(fù)部位的新焊縫進(jìn)行測試。應(yīng)力測試分別在新焊縫振動前、振動后進(jìn)行,振動前與振動后各取3組數(shù)據(jù),并分別對其進(jìn)行歸納,得出振前后應(yīng)力變化曲線。兩組曲線對比后,得出新焊縫殘余應(yīng)力在振動前后的應(yīng)力變化。測試結(jié)果如圖2所示,圖中σx、σy分別為新焊縫橫向殘余應(yīng)力和縱向殘余應(yīng)力。 圖2 新焊縫振動前和振動后測試曲線測試結(jié)果表明,新焊縫無論是在垂直于焊縫方向還是在平行于焊縫方向的殘余應(yīng)力在振后都有減小,兩個方向上的殘余應(yīng)力減小范圍均在50%以上。
結(jié)論: (1)振動時效處理降低了再生器焊縫殘余應(yīng)力,其減小范圍在50%以上,效果比較理想。
(2)對于大型工件采用振動時效方法降低焊縫殘余應(yīng)力效果顯*,并大大縮短了檢修工期,該方法對于石油化工領(lǐng)域設(shè)備現(xiàn)場維修具有普遍意義。
(3)一年多來,設(shè)備運行正常,各項技術(shù)指標(biāo)均達(dá)到設(shè)計要求。